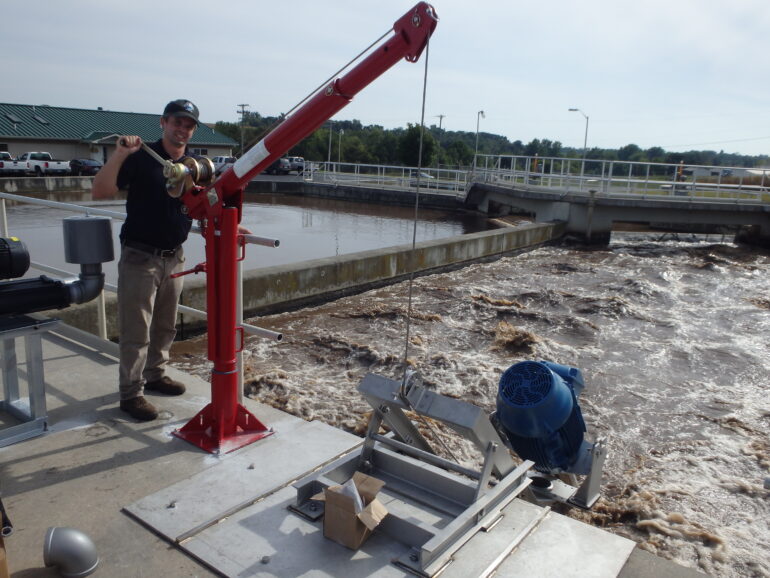
Through conversations with plant operators and personal experience servicing aeration equipment, the Aeration Industries’ team recognized the great importance of maintenance and safety for those servicing wastewater aeration equipment. The idea to develop a mount on a sliding pedestal with the goal to allow operators to maintain equipment safely on the walkway was derived. The secondary goal was to reduce the cost of maintenance and give plant operators the ability to service equipment on their own versus having to hire service teams. The Aeration team also understood that plant operators are also facing strict permit limits, allowing for less downtime for maintenance and repairs, so maintenance would need to be done efficiently without having to shut down the whole plant.
Conventionally installed aeration equipment often requires a difficult and time-consuming maintenance effort. Traditionally, surface mounted equipment relieves a portion of these issues, as all working components are readily available for full service without shutting down operations. Float mounted surface aerators pose unique maintenance challenges; servicing from within the basin, the requirement of cranes, and the need to move equipment to the shoreline or basin perimeter.
To address these unique concerns, Aeration Industries® International developed the maintenance friendly mounting option; the Aire-O2™ Universal Mount. With the use of a patented slide design and a low cost “mini-crane”, the aerators are hoisted and pivoted in a position that allows for simple service. The sliding mechanism allows the unit to move through varying water depths, creating a design that combines operational flexibility with ease of maintenance.
Easing Maintenance
The Universal Mount is an all stainless steel mounting structure, which is partially submerged and installed on walls or walkways of wastewater treatment basins. The structure has a sliding pedestal with rollers with a solid bearing. The solid bearing has no moving parts like needle bearings, so it provides superior durability in harsh wastewater environments, especially in a submerged condition. The sliding pedestal travels on a 45-degree track that allows the aerator to be positioned at the desired height depending on the freeboard. On the sliding pedestal, there is a pivoting tube that allows the aerator to point in any direction to form the ideal flow that will keep the solids suspended efficiently. The sliding pedestal is pulled up and down by a cable which runs on a pulley that sits on top of the track. The pulley is engaged by a hand winch that is integrated into the mounting system. The hand winch and its pedestal is designed to be portable. Multiple universal mounts can share one hand winch for bringing the unit up and down. Universal Mount only requires four anchor bolts on top and two anchor bolts on the front to complete the installation of the mounting system.
When maintenance is due, the Universal Mount allows operators to access the unit without a boat or renting a crane, allowing for safe and efficient maintenance. The whole process of bringing the aerator into the maintenance position takes no more than 10 minutes.
The Universal Mount in Practice
The wastewater treatment plant in Elizabethtown, Pennsylvania, selected Aeration Industries’ Aire-O2 Triton® aerator/mixers coupled with Universal Mounts to replace aging rotors. Prior to the replacement, Elizabethtown had an oxidation ditch with six rotors. The rotors were not fully aerating the tank due to welds and bolted sections of the baffles failing and falling into the bottom of the ditch. With a fourteen-foot-deep ditch, it was very important that the treatment was occurring throughout the entire volume of the ditch.
Access to the rotors was also very challenging for cleaning rags and other debris off the shaft and blades. To pull the rotors out, the operator had to pull the motor, gearbox, and the seal plates at each end. Their rotors also had several problems with motor and gearbox failures, requiring the city to spend a lot of money to keep the rotors up and running. It was often a full day of work to maintain or fix one rotor.
The operator at Elizabethtown was looking for a new type of aerator with easy access for maintenance and repairs. Two Aire-O2 Triton aerators with the Universal Mount were installed so the operator could determine if the mounting systems were what he was seeking. Installation went smoothly; the mounting holes for the mount were pre-drilled before installation day and it only took half a day for the two mounts to be installed on the existing concrete walkway where the rotors were originally mounted. The mounting installation also did not require the removal of existing rotors.
The electrician was pleased with the mounting system since all the wiring could be done while standing right on the walkway; bending over and reaching out over the water was not required for setup. When it came time for maintenance, the operator only needed to crank the unit up with a hand winch that is part of the mounting system. It took the operator 1 to 2 hours to do the maintenance on the walkway for each unit. This was much less time spent on maintenance than his previous experience with the rotors.
After running the Tritons on the mounts for approximately eight months and seeing the performance of the aerators, along with testing the ease of maintenance of the mounting system; the plant operator decided to install eight more aerators. He decided to do a one for one replacement for the previously operating rotors. Now, all ten aerators (five in each ditch) have been up and running for about a year with the mounting systems in place.
A month after startup with all ten aerators running, the plant saw such successful mixing that they had to waste significantly more sludge than with their previous systems. They are also seeing better treatment, specifically lower TN numbers, which is due to the entire volume of the basin being aerated.
Denny Bair, Elizabethtown’s plant operator, said the mounting system “is simply the best of the best.” He has not only reduced time spent on maintenance, but is noticing that the whole water column is aerated versus just the top six feet he was previously seeing with the brush rotors. This has led to improved dispersion and reduced settling.
A broken-down and out of service diffused aeration basin located just outside of Johannesburg, South Africa, needed a new treatment solution. Use of the existing basins with obstructions was a requirement, as well as simple access to the equipment without the need to empty the basin or the use of large cranes for equipment maintenance or repairs. Using Aeration Industries’ Triton process aerator and mixer with the Universal Mount provided an aeration and mixing solution allowing for 180° of rotation. Basin optimization was not the only success; through the use of Variable Frequency Drives and Oxygen Sensors, the client kept solids in suspension and reduced energy costs.
Safety
One of the primary concerns the Aeration Industries team aimed to address with the improved mounting system was increasing safety when maintenance is required on aeration equipment. The Universal Mount addresses this need, as operators never need to be in the water to service the equipment; everything can be done safely on the walkway. Reaching over the water has also been eliminated.
The mount also diminishes the need for operators to drain the basin or climb down onto the equipment to make repairs. This reduces risk of injury while also simplifying the maintenance process.
Health was an essential concern, as well. The risk of Legionnaires’ disease (severe form of pneumonia caused by legionella bacterium) is high with other technologies, if wastewater splashes and creates a mist that is ingested by operators. The Aire-O2 Triton does not create any splashing or mists and the mounting system does not require operators to be over the water; nearly eliminating all health risks.