Industrial MBR solutions
Ivanhoe Cheese
A Solid Solution and Impeccable Service Wins Over This Client.
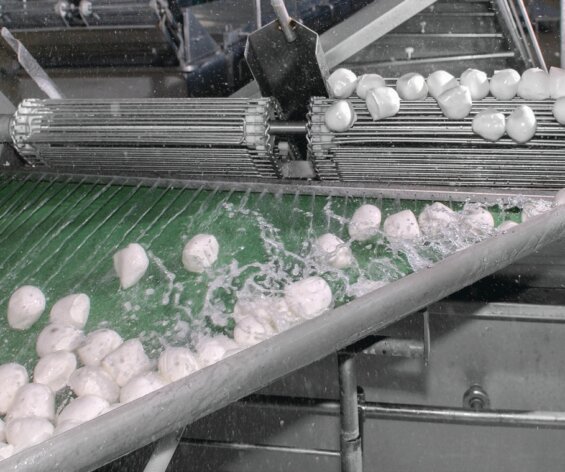
Canada’s oldest cheese company looks to Newterra for systems and support
Industry
Dairy Manufacturing Facility
Location
Madoc, Ontario, CA
Capacity
11,883 GPD (45 m3/day)
Installed
2022
THE CLIENT
Ivanhoe Cheese
A need for an MBR Industrial Sewage Treatment Plant
Ivanhoe Cheese, a member of the Gay Lea family, is a growing and successful cheese company known for its commitment to quality and customer service. Established as a cooperative in 1870, it is the oldest cheese company in Canada and holds HACCP, Kosher, and Halal certifications.
CHALLENGE
An expansion and the introduction of more stringent government regulations
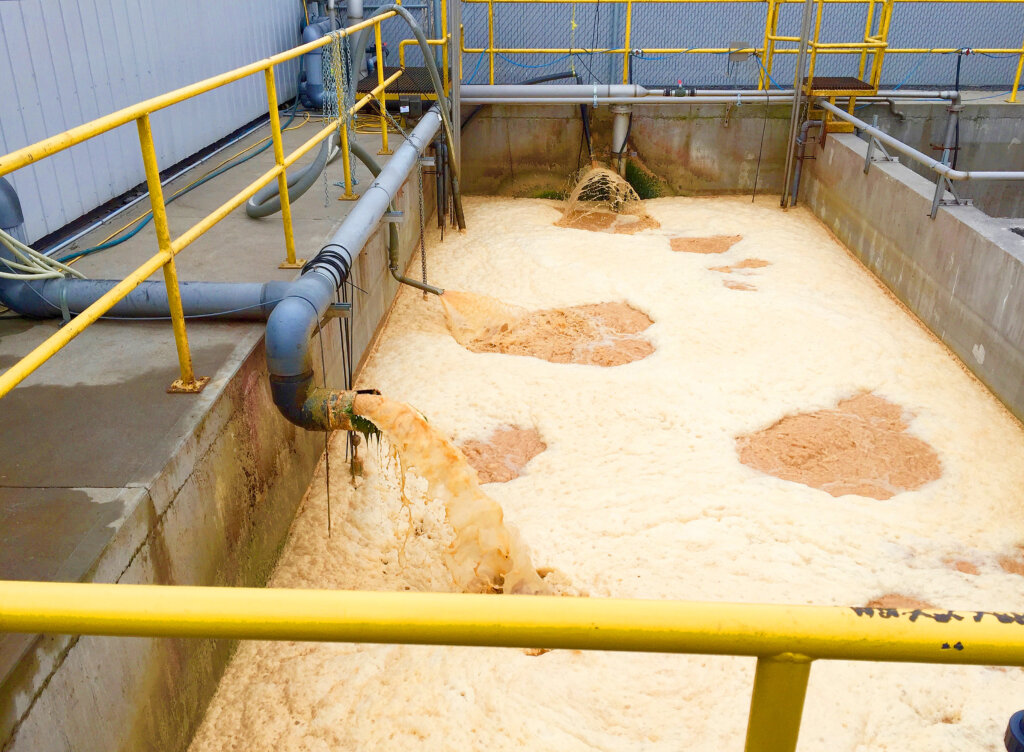
Historically, the Ivanhoe Cheese facility managed its high-nutrient wastewater by spraying it onto surrounding agricultural land. However, the introduction of stricter government regulations, which would eventually prohibit this practice, prompted the company to explore alternative treatment solutions to ensure ongoing environmental compliance.
Later, the Ivanhoe Cheese facility began receiving a new source of milk for whey production. Whey, a by-product of the cheese-making process, is separated from the solid curds during production and has various applications in the food industry, including use in the production of various food products.
To produce concentrated whey, milk is processed through a Reverse Osmosis (RO) system, which separates the whey—a liquid containing water, lactose, proteins, minerals, and some fats—from the excess wastewater. The separated wastewater is then sent to the MBR (Membrane Bioreactor) system for treatment and discharge.
The additional permeate from this process required additional treatment capacity.
SOLUTION
Newterra’s MBR solution was selected for its simplicity and its high effluent quality.
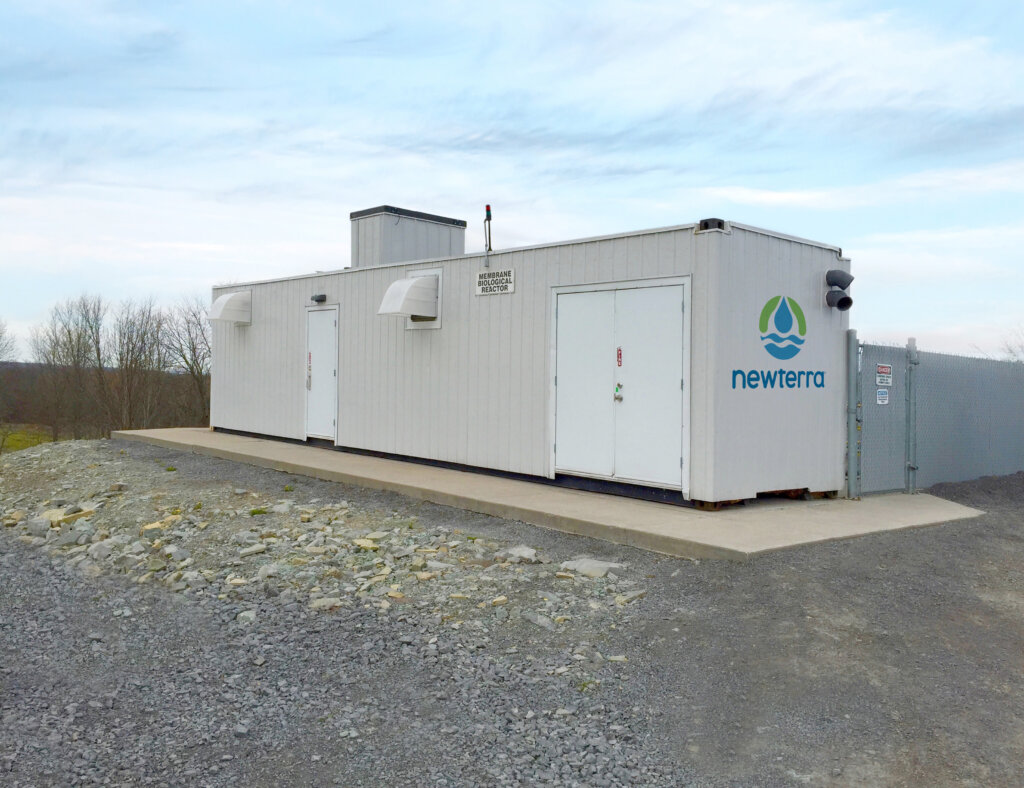
After evaluating various treatment technologies, Ivanhoe Cheese selected Newterra’s Industrial MBR (Membrane Bioreactor) system for its simplicity and ability to produce high-quality effluent. The system was designed to handle a flow rate of 11,883 GPD (45 m³/day), with approximately 90% of the wastewater coming from cheese production and the remaining 10% from domestic wastewater within the facility.
To address the high organic load (influent BOD levels of approximately 3,000 mg/L), the system incorporated extended aeration, enabling the facility to continue direct discharge into a weeping bed. The system also provided the potential for water reuse in cooling towers and boilers.
The core of the MBR system was housed in a 40-foot, ISO-certified shipping container containing the membrane tanks, control systems, and blowers. Below-ground tanks were used for aeration, offering key advantages such as space efficiency, environmental control, improved safety, and aesthetics.
Recognizing the need to manage fats, oils, and greases—by-products of cheese production—Ivanhoe Cheese also implemented a Dissolved Air Flotation (DAF) system. This technology is particularly effective in applications where traditional sedimentation methods may be less efficient or where high-quality treated water is required. Initially installed as a temporary rental system for compatibility testing, the DAF system exceeded expectations and was later replaced with a permanent Newterra DAF system.
As the facility expanded its operations to process additional milk for whey production, wastewater volumes increased. To accommodate the additional permeate from the whey process, Ivanhoe Cheese installed a second 40’ ISO-certified shipping container MBR system, effectively doubling treatment capacity for rapid scale-up.
Since this additional permeate introduced more clean water into the system, extra membranes were added to handle its removal efficiently. However, the aeration in the wastewater holding tanks remained unchanged, as the overall pollutant load did not increase. Instead, the membrane capacity had to double to process nearly twice the volume of water through the system.
SERVICE MAKES THE DIFFERENCE
A Seamless Startup and Lasting Support: Ivanhoe Cheese’s Experience
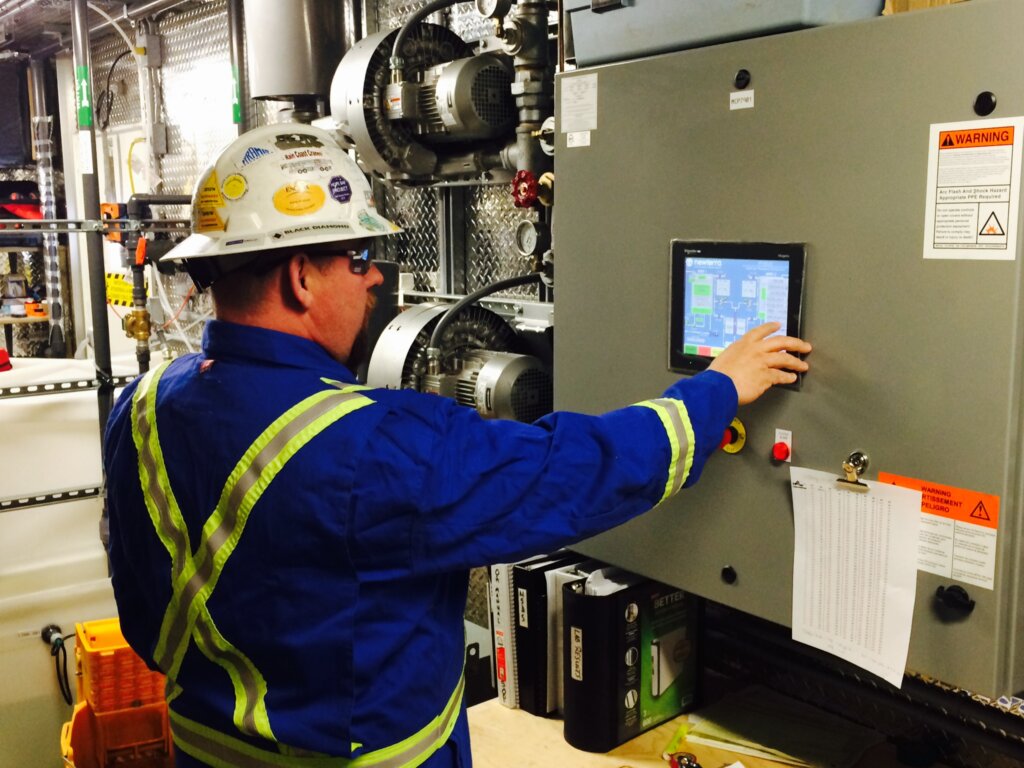
When Ivanhoe Cheese expanded its operations, adding new wastewater treatment technology was a necessary step to meet regulatory requirements while maintaining efficiency. With new systems in place, getting up to speed was critical.
Newterra’s Field Service team spent several days on-site, working alongside Ivanhoe Cheese personnel to review equipment, fine-tune operations, and provide hands-on training to ensure a smooth startup. For Campbell Thomson, the experience was exceptional:
“Eddy and the crew … were great to work with, knowledgeable and an overall pleasure. I feel lucky to have had such a great experience training with these guys.”
— Campbell Thomson, Ivanhoe Cheese – Gay Lea Foods
The support didn’t just make installation easier—it gave the Ivanhoe team full confidence in operating their new system independently. Chris Spencer described how valuable the process was:
“We want to express our thanks to Newterra for the great team of guys that came for the startup … those kind of people are invaluable to get us going on the right track… [We] were very confident we could operate this 100% when Eddie cut us loose on Saturday!!!”
— Chris Spencer, Ivanhoe Cheese – Gay Lea Foods
The collaboration didn’t end there. Impressed with the startup and training experience, Ivanhoe Cheese chose to continue working with Newterra for ongoing support services, ensuring their system remains optimized for long-term performance.
For Ivanhoe Cheese, the startup process wasn’t just about installing equipment—it was about gaining the knowledge, support, and confidence to run their wastewater treatment system successfully from day one.
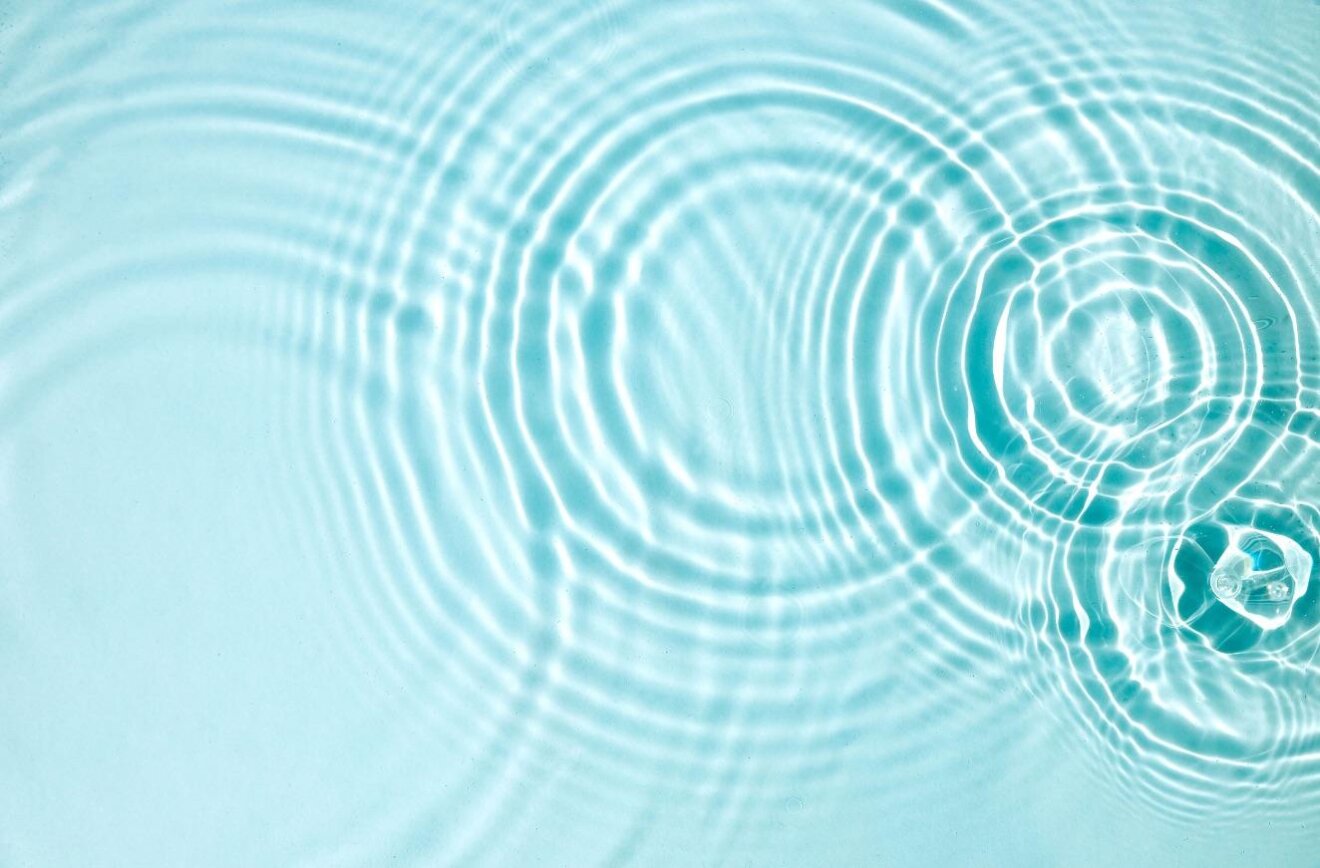
We Are Here to Help
Partner with Newterra to maximize your water resources. Together, we’ll design solutions specific to your needs in the food and beverage industry, boosting your efficiency and driving success.